A Role of ISO 9001 Certifications in Quality Assurance
In today's competitive landscape, businesses are constantly searching for ways to improve their credibility and improve their processes. One successful way to achieve this is through ISO 9001 certification. certifyproinsights.ma acknowledged standard centers around quality management systems, permitting organizations to guarantee they fulfill customer and regulatory requirements reliably. By gaining ISO 9001, firms can not only increase efficiency but also foster a culture of continuous improvement.
ISO 9001 certification shows a commitment to quality and excellence, offering organizations a framework to simplify their operations. This standard assists businesses establish robust processes, reduce waste, and enhance customer satisfaction. Consequently, achieving ISO 9001 certification can serve as a significant distinct advantage in the marketplace, luring new clients and keeping existing ones while cultivating a solid reputation for reliability and quality assurance.
Comprehending ISO 9001 Certification
ISO 9001 certification is an internationally recognized standard that defines the requirements for a quality management system. Organizations that secure this certification show their commitment to perpetual improvement and customer satisfaction. The standard offers a framework for companies to ensure they reliably provide products and services that satisfy customer and regulatory requirements, ultimately improving overall efficiency and effectiveness.
To obtain ISO 9001 certification, an organization must establish a quality management system that complies with the particular criteria stated in the standard. This involves thorough logging of processes, regular assessments of objectives, and a clear emphasis on customer feedback. The certification process typically includes a comprehensive audit by a independent certification body that validates compliance with the ISO 9001 requirements.
The value of ISO 9001 certification goes beyond compliance. It serves as a strategic tool that helps organizations establish a strong foundation for operational excellence. By focusing on quality management principles such as guidance, systematic approach, and consideration of risks, companies can enhance their reputation, boost efficiency, and foster a culture of continuous improvement.
Benefits of ISO 9001 in Quality Assurance
ISO 9001 is vital in boosting organizational quality assurance by creating a system for reliable quality management practices. This certification assists organizations define and implement processes that ensure products and services meet customer and regulatory requirements. By following these processes, organizations can reach higher levels of customer satisfaction, resulting in increased loyalty and repeat business.
Another important benefit of ISO 9001 is the advancement of efficiency in operations. The certification encourages organizations to identify waste and always pursue betterment. By promoting a culture of ongoing enhancement, businesses can optimize workflows, reduce waste, and improve product quality, which often results in cost savings and enhanced overall performance.
Furthermore, obtaining ISO 9001 certification enhances a company's credibility and market edge in the market. Being ISO 9001 certification is known internationally and shows a commitment to quality and excellence. It gives confidence to customers and stakeholders that the organization adheres to internationally accepted quality management practices, setting it apart from competitors and possibly creating opportunities for new business opportunities.
Steps to Achieve ISO 9001 Certification
The process to achieving ISO 9001 certification begins with a dedication to quality assurance principles. Organizations must initially familiarize themselves with the requirements detailed in the ISO 9001 guideline. This involves understanding the extent of the certification and assessing how it applies to your specific operations. A thorough deficiency analysis can be performed to spot areas where existing procedures may need improvement or alignment with the standard.
Once the essential knowledge has been obtained, the following step is to create and implement a quality assurance system that meets the criteria of ISO 9001. This includes setting up recorded policies, guidelines, and procedures that facilitate reliable product and service delivery. Employees should be involved in this initiative through instruction and awareness efforts to ensure all employees understands their duties in maintaining quality metrics.
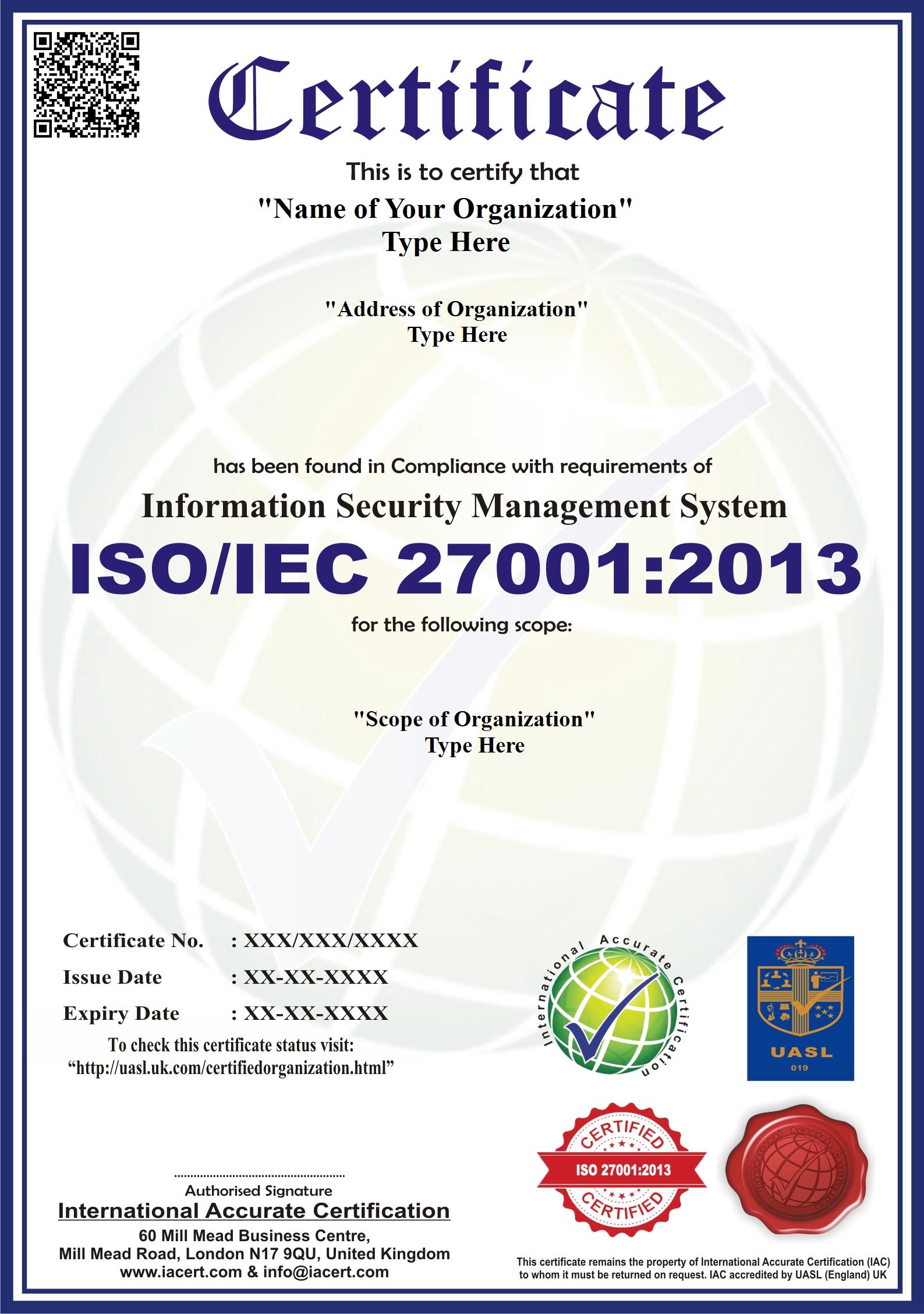
After effectively adopting the QMS, organizations must organize for an self audit to evaluate their conformance with ISO 9001. This audit assists identify any nonconformities and areas for more improvement. Following the internal audit, management reviews the QMS to ensure its efficacy. Once all corrections have been taken, the organization can then request certification through a recognized certification body, commencing the third-party audit process that will lead to ISO 9001 certification after successful completion.